How to control the radial clearance of bearings
The internal clearance of a bearing refers to the total distance that one bearing ring can move radially or axially relative to the other bearing ring. For the clearance of bearings, it is necessary to distinguish between the initial clearance before installation and the working clearance after installation and reaching its operating temperature. The initial clearance of a bearing is generally larger than its working clearance due to the tolerance fit of different interference amounts, as well as the varying degrees of thermal expansion between the bearing ring and its adjacent components, resulting in ring expansion or compression.
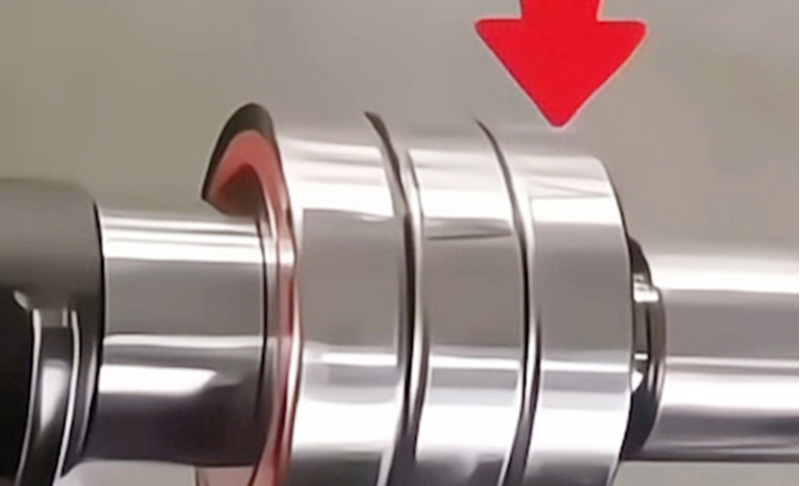
In order to ensure the good operation of motor bearings, radial clearance is very important, which requires selecting suitable bearings to match according to the actual characteristics and operating conditions of the motor. The general principle of bearing operation is that the working clearance of ball bearings should be zero or slightly preloaded; But for cylindrical roller bearings, there must be a certain amount of residual clearance during operation.
Under normal working conditions, selecting ordinary group clearance bearings can obtain suitable working clearance. However, when the working and installation conditions differ from the general situation, such as when the inner and outer rings of the bearing are interference fit, or when the temperature difference between the inner and outer rings has a significant impact, bearings with a larger or smaller clearance than ordinary groups should be selected.
Radial positioning and control points of bearings
In the actual process of bearing selection, some motor manufacturers are accustomed to choosing bearings with high load-bearing capacity, but often encounter bearing noise problems, especially for some motors. When running under no-load, the bearing noise is loud, but when running under load, the sound is particularly good. This problem may be related to improper bearing selection, which makes the bearing have ideal axial positioning, which is a necessary condition for good bearing operation.
From the analysis of the operating characteristics of bearings, in order to fully achieve the bearing capacity of the used bearing, the entire circumference of the inner and outer rings of the bearing, or the shaft ring and seat ring of the thrust bearing, must be fully supported with firmness and uniformity. The supporting surface can be a cylindrical or conical surface, and for the shaft ring and seat ring of the thrust bearing, a flat surface should be applied. Therefore, the machining of the surface that matches the bearing ring must achieve a certain level of accuracy and should not have any grooves, holes, or other discontinuous shapes. In addition, the bearing ring must be securely fixed to prevent rotation between its mating surfaces under load.
Generally speaking, a suitable interference fit is necessary for the bearing ring to be fixed in the radial direction and receive sufficient support. If the bearing ring is not properly or sufficiently fixed, it can easily cause damage to the bearing and related components. But sometimes for the convenience of installation and disassembly, or for bearings that require axial movement due to their use in floating ends, interference fit cannot be used. In some cases where clearance fit is used, special measures need to be taken to reduce wear caused by creep, such as hardening the mating surface and shoulder of the surface hardened bearing, lubricating the mating surface and eliminating wear particles through special lubrication grooves, or using the positioning keyway on the side of the bearing to fix the bearing.